Sprayed graded electrodes
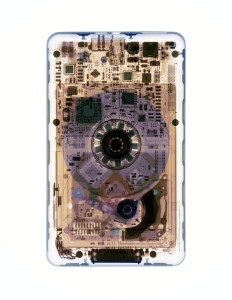
Developments in Oxford aim to enable electrodes to be fabricated using spray deposition that will allow the porosity and other characteristics to be varied in a controlled fashion through the electrode thickness.
These developments will facilitate better performance of existing battery chemistries and the commercialisation of new battery chemistries.
Lithium-ion batteries
Lithium-ion batteries (LIB) are a mature, stable market with around 3 billion cells produced per annum for use in consumer, industrial and automotive applications. LIBs are relatively simple energy storage devices produced using a manufacturing process that is both productive and scalable.
Frost and Sullivan estimated the LIB market size to be US$18bn in 2013, growing at 21% CAGR. Despite the market size, today’s bestselling batteries use essentially the same chemistry as that invented in Oxford by Goodenough and colleagues in 1980, and the same manufacturing process.
Limitations of current LIB manufacture
Current lithium ion battery (LIB) electrodes are ‘monolithic’ in that the electrochemically active materials that are used in powder form in the electrodes, and the residual porosity between the powder particles, are constant through the electrode thickness. Despite their known benefits, graded electrodes are not commercially available because a scalable manufacturing technology has not been developed.
Recent developments in Oxford aim to enable electrodes to be fabricated using spray deposition that will allow the porosity and other characteristics to be varied in a controlled fashion through the electrode thickness. This facilitates both better performance of existing battery chemistries and the commercialisation of new battery chemistries.
Oxford technology– sprayed graded electrodes offers performance advantages
Oxford’s technology is scalable, allowing LIB manufacturers to spray electrodes from a variety of suspensions. Thin, flexible electrodes (100’s nm to 10’s mm) can be produced and various nanomaterials can be introduced into the electrode at any point. The spraying process allows the electrodes to be graded in different ways. Recent literature suggested that in theory, a capacity increase of up to 70% might be possible over conventional slurry-cast LIBs if graded particle and porosity distributions were available.
Improvements in thinness and flexibility fit well with requirements for LIBs in mobile electronics while improved energy density and the possibility of using safer electrolytes suits transport applications.
Request more information if you would like to discuss this further.
about this technology