Commercial nanofibre production: Stellenbosch University
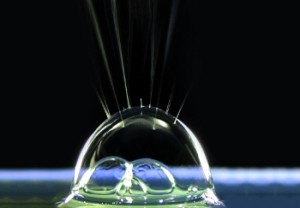
Marketing clever technologies which make large scale, inexpensive nanofibre manufacturing possible.
Isis assisted Stellenbosch University in South Africa to bring their innovative nanofibre manufacturing technique to market by developing strategy and making the right contacts with companies involved in nanofibre development and manufacturing.
Stellenbosch is recognised as one of the top research universities in South Africa. The team of researchers from Stellenbosch invented a family of clever technologies that finally make large scale, inexpensive nanofibre manufacturing possible. Stellenbosch launched a spin-out company to further develop these technologies and is negotiating licensing and joint development agreements with several large multinational companies.
The newly invented bubble electrospray process enables the manufacture of very large quantities of aligned nanofibres and continuous spinning of the fibres into yarn. This process works for a wide range of materials and applications, with either water or solvent based solutions. The research team have successfully spun fibres from a number of polymers, carbon precursors and other compounds. By using surfactants to stabilise the bubbles, large numbers of nanofibres can be extracted simultaneously.
For those liquids that do not easily form bubbles, the Stellenbosch team has invented what they refer to as ‘solid bubbles’. This technology uses solid glass spheres that are continuously rotated through the desired solution. The nanofibres are extracted by an electric charge from the surface of the spheres in the same manner as from the ordinary bubbles, allowing nanofibres to be spun from a very wide range of substances.
The Stellenbosch researchers have also invented a novel antimicrobial polymer compound that can be spun into nanofibres that are intrinsically antimicrobial, opening up a wide range of potential new healthcare products, as well as air and water purification applications.
Nanofibres have captured the imagination of researchers for decades now. Many potential applications have been identified including better composite materials, advanced membrane and filter materials and a variety of potential medical products. However, the inability to manufacture large quantities of nanofibres economically has held back these technologies from achieving their potential.
Using the Stellenbosch process, the diameter of the nanofibres can be controlled by varying the viscosity of the solution and the size of the bubbles or spheres. Projections indicate that the bubble electrospinning process could produce fibres at rates of between 500g and 5kg per hour per square metre of spin-bath surface area, depending on polymer and spin solution concentration.